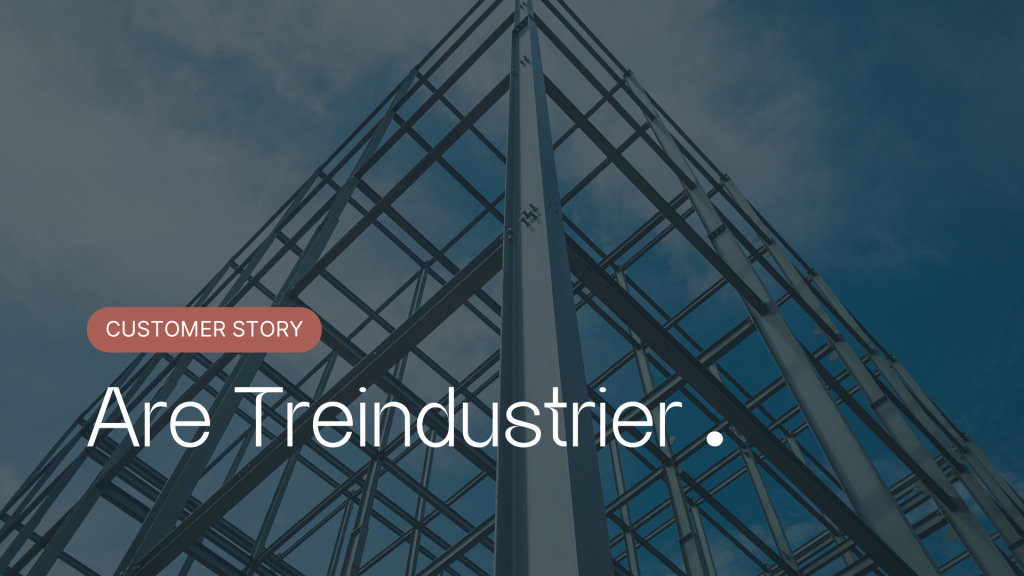
Are Treindustrier invests in RamBase Cloud ERP
It is not uncommon for us at Arribatec to be in dialogue with manufacturing companies that have used more traditional accounting systems as business solutions. The consequence is often that you have to create manual and self-developed additional solutions (in many cases this solution is called “excel”) to support key processes in the company. Enough is enough, and Are Treindustrier is ready to take the step into RamBase Cloud ERP and gain greater efficiency in its core processes.
Who is Are Industrier?
Are Treindustrier is your competence partner for wooden structures. They are one of Norway’s leading suppliers and manufacturers of prefabricated wooden structures. Their focus is “the right product at the right time with a focus on design, functionality, cost-effectiveness and sustainability”. Are Treindustrier produces locally in Askim and Kaupanger.
What ERP challenges do they want to improve with RamBase Cloud ERP as a solution?
- Get rid of excel, excel and excel: Are Treindustrier works a lot in excel, which often means many cumbersome and person-dependent processes. Here, standardised support using best practice processes is desirable.
- Integration with design (Pamir): Today, the Pamir solution, an industry solution, is used in the design phase of wooden structures. In the traditional sense, Pamir works as a CAD/PDM solution where engineers draw and generate bills of materials (BOMs), which forms the basis of purchase and production orders.
With Arribatec’s expertise, Pamir now integrates seamlessly with RamBase, so that bills of materials and sales orders automatically flow between the systems. This will give Are Treindustrier the opportunity to work more efficiently, with better control and without unnecessary manual processes. This will strengthen the collaboration between design, sales and production. - Purchasing and warehousing: Previously, purchasing processes were characterized by manual routines, which led to inefficiencies and limited overview. With the transition to RamBase Cloud ERP, Are wants to achieve better control of the warehouse through functions such as minimum stock and automation in notifications when new purchases are needed based on orders, productions and forecasts. Procurement processes are improved by using the “Material Requirements Planning” (MRP) module, which ensures that the right number of items are purchased at the right time, based on demand and available stock status.
In addition, RamBase offers effective tools for managing and following up on changes to purchase orders, such as adjustments in delivery dates and handling delays. The system gives buyers access to real-time data, making it easier to communicate with suppliers and make quick decisions in the event of deviations. Other features, such as tracking purchase history, following up on appointments, and quality of delivery, contribute to a more proactive and efficient workflow for buyers. This provides a safe and controlled process that reduces the risk of delays and errors in the value chain. - Improved traceability in production: It is important for Are to have control over which raw materials are used in production. By using barcodes and terminals, they can now quickly and efficiently gain control of this. It will help them with traceability in any deviation situations because they have easier insight into “who, what, when and where”. Advantages of this will be to improve own processes in production, but also for documentation to suppliers in the event of complaints etc.
In addition, this meets increasingly stringent demands from customers for traceability and quality in production, which can strengthen their competitiveness and trust in the market. A concrete example of this could be avoiding the use of certain materials in certain contexts. With RamBase, for example, it will be possible to trace serial numbers/batch numbers used in production, back to goods receipts and purchase orders. - Control of hours spent in production: Until now, Are Treindustrier has had a manual planning process based on experience. With Rambase, planned time will flow seamlessly from the Pamir feed system to production orders in RamBase, and form the basis for production planning. The “Visual Production Planner”, an option for the module, will be used for simpler, visual planning and moving operations between the four production lines. This is managed on the basis of available capacity. For the first time, Are Treindustrier will be able to register accrued time in production, which provides new insight and a better data basis for costing. In addition, it will help to streamline production processes and improve cost control.
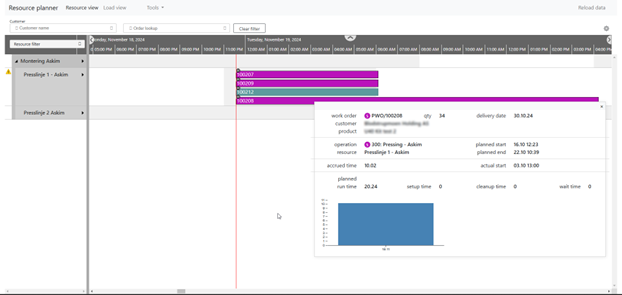
Visual Production Planner: This intuitive planning tool gives you a quick overview of available capacity for new jobs, helps you identify potential bottlenecks, and allows you to easily make necessary changes using drag-and-drop functionality.
6. Finance and control: Previously, Are used a traditional, ground-based accounting and logistics solution. With RamBase, they look forward to a comprehensive solution where everything is connected and where the accounts are naturally created as a consequence of processes from sales, production, purchasing and logistics. Manual journal entry will be minimized, and the integrated general ledger module will, among other things, efficiently match incoming invoices with purchases and goods receipts. This is one of the areas where Are Treindustrier will reduce unnecessary time spent.
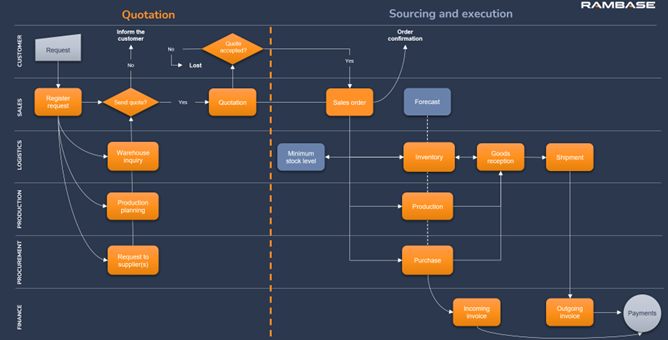
Rambase Cloud ERP – Complete Quote2cash solution “(from request to payment”).
Focus on successful implementation:
The transition to a cloud-based ERP system for Are Treindustrier should not be underestimated. Today’s solutions are manual and incorporated, and it is important that both parties take great responsibility for ensuring the smoothest possible transition to new, standardized processes in a cloud-based system. It provides a good starting point for further discussions and solution design that we are together onsite, so that Arribatec as a supplier gets a practical understanding of processes and wishes for future solutions, with the customer.
Vinoshan Mani, RamBase consultant at Arribatec, praises Are Treindustrier as a customer: “They have been very involved and dedicated in the process, and among other things, taken testing of processes seriously. This is greatly appreciated by us consultants and often makes projects more efficient, successful and fun,” he says.

Important to understand the business: Arribatec consultants Vinoshan Mani and Anders Blom out on a tour together with Daniel Iversen, sales engineer and Pamir manager at Are Treindustrier.
About the collaboration and the way forward with Arribatec:
Arribatec uses its implementation methodology to ensure an efficient process from mapping meetings, configuration, training, testing and commissioning to support the start-up.
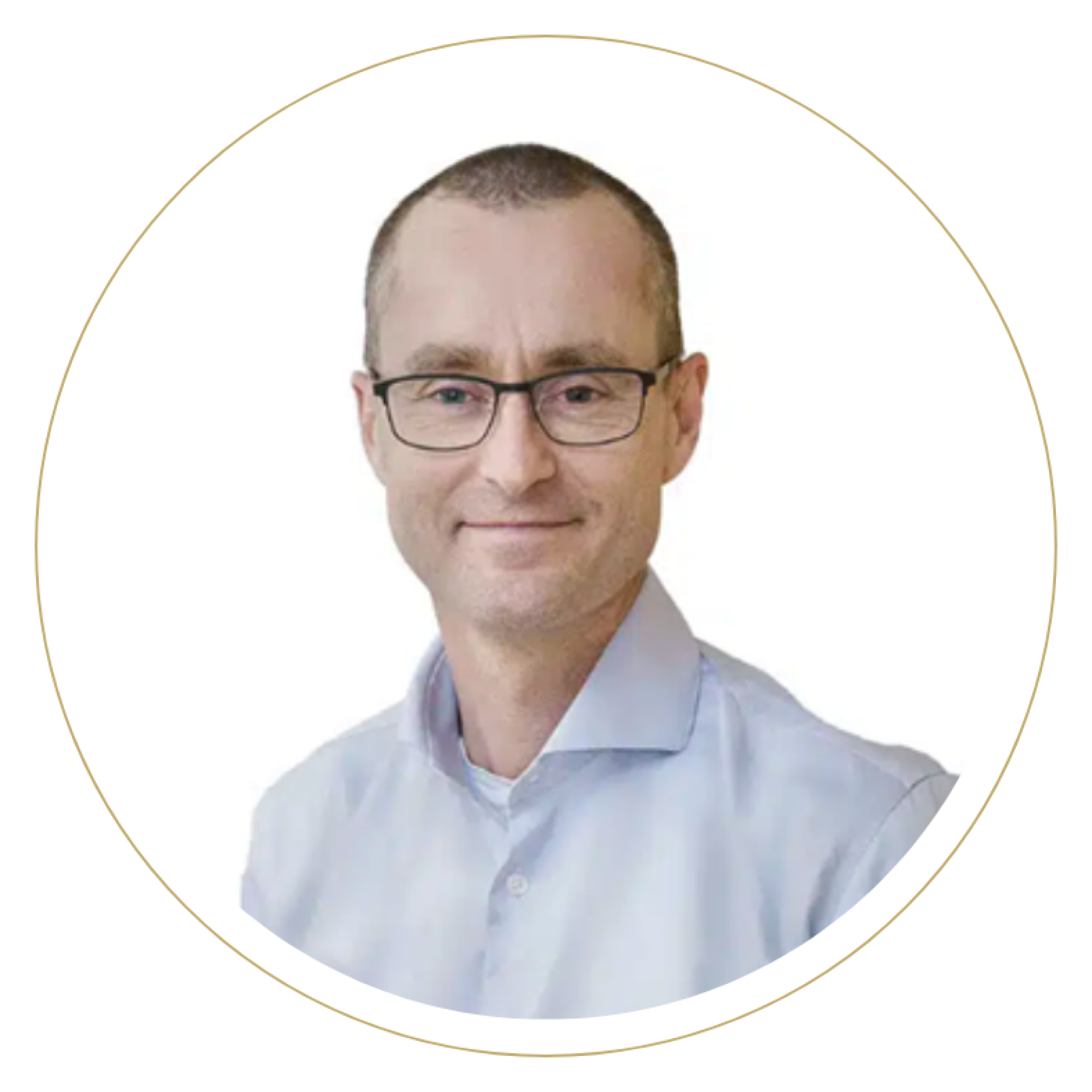
“We look forward to streamlining core processes on a modern ERP platform and facilitating further growth”
“The implementation of RamBase has so far been very positive, and we have a great collaboration with the project manager and consultants. The close follow-up from Arribatec has reassured us and together we have come up with solutions that secure our needs in a standard system.
Another strength we see at Arribatec is their expertise in integration, so that they take overall responsibility that also includes the interaction with our pre-system Pamir. This means that we have one point of contact when needed.
We look forward to streamlining core processes on a modern ERP platform and facilitating further growth,” says Egon Lundsrud in Are Treindustrier.